L1A1Rocker
Active Member
One of my on going projects is a Form 1 SBR in 300BLK. I made a custom break (or is that brake?) that will also be used as a QA/QD point for a silencer (another of my on going Form 1 projects). Anyhow, I wanted the brake to just tuck in the handgards. But that meant a custom length barrel. Sooo, I finally got off my duff and chopped off three inches from a 10.5 barrel I've had waiting for this project.
Next step is to parkerize the brake and the exposed metal on the barrel.
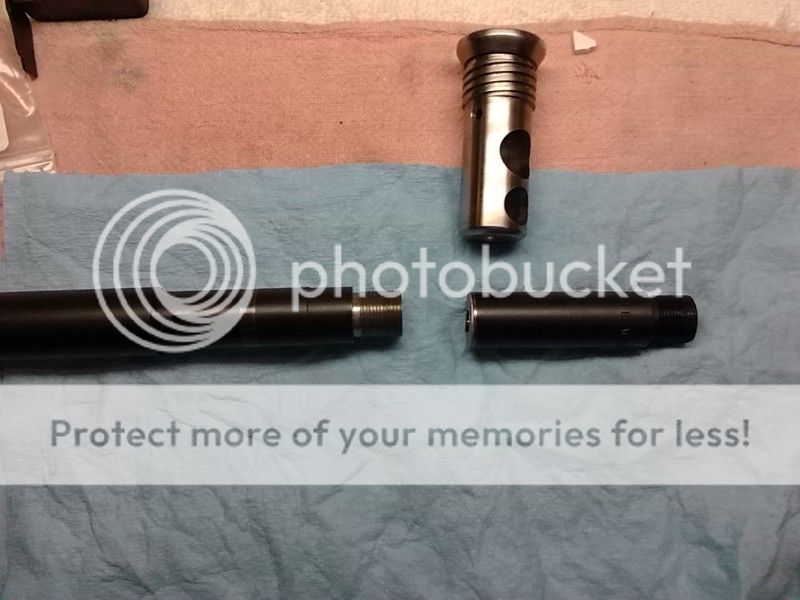
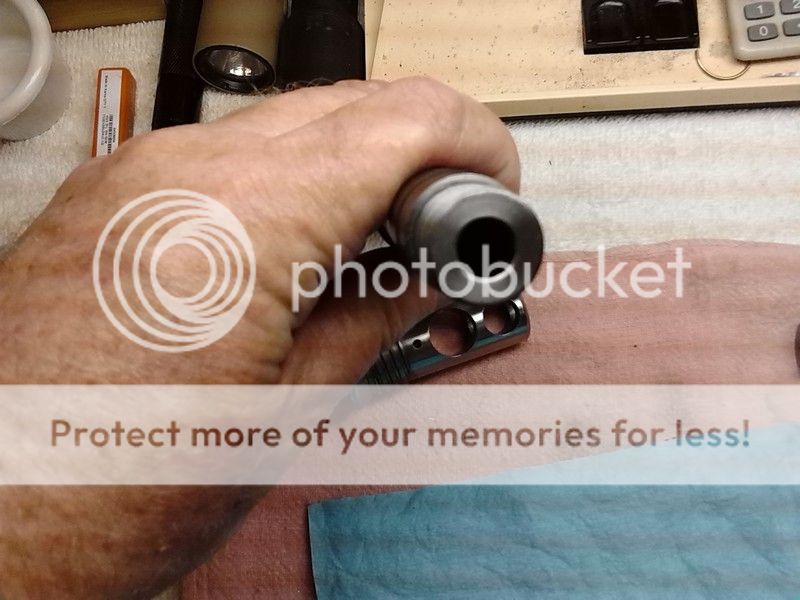

Next step is to parkerize the brake and the exposed metal on the barrel.