I have been fighting base flashing on bullets from the 2 cavities farthest from the pivot pont on my 4 cav brass MP 452200 swc mould.
The mould didn't do this when new, it seems to have started recently.
Even the top bullet has a hint of flashing but far less than the other two.
No major signs of galling or wear around pivot point on top of mould. I keep it well lubed with Ester 100 AC oil
You can see light between sprue plate and mould surface. I have the plate pretty loose, I can easily swing it with my little finger. MP places a small bushing in the plate pivot hole so over tightening can only go so far as the bolt begins to compress the bushing without putting much more tension into the plate.
Any ideas on what to do to make this stop? It does seem to improve at some mould temps, I just haven't been able to find a tempo that can stop it.
The mould didn't do this when new, it seems to have started recently.
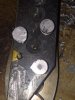
Even the top bullet has a hint of flashing but far less than the other two.
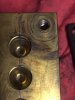
No major signs of galling or wear around pivot point on top of mould. I keep it well lubed with Ester 100 AC oil
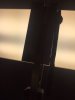
You can see light between sprue plate and mould surface. I have the plate pretty loose, I can easily swing it with my little finger. MP places a small bushing in the plate pivot hole so over tightening can only go so far as the bolt begins to compress the bushing without putting much more tension into the plate.
Any ideas on what to do to make this stop? It does seem to improve at some mould temps, I just haven't been able to find a tempo that can stop it.