KeithB
Resident Half Fast Machinist
Heat Treating Steel
What is steel?Basic steel is a solution of iron (an element) and carbon (an element). Just as sugar or salt can be dissolved in water, carbon can be dissolved in iron. The maximum amount of carbon that can be held in solution is 1.73% by weight. Any carbon in excess of that will clump together as graphite in the form of flakes or other shapes and is called cast iron. If you break a piece of cast iron and rub it against a clean white rag you will see a silvery smear which is the exposed carbon on the surface. Most cast iron has anywhere from 2% to 5% carbon.
Alloy steel consists of iron and carbon and other metallic elements such as chromium, vanadium, etc. Alloy steels have been developed to improve the properties of basic steel such as increasing the strength, making it more ductile, imparting corrosion resistance, or making it easier to heat treat.
We will deal with basic steel first.
Microstructure of steel
Basic steel can have five phases or microstructures (the arrangement of atoms). The softest phase is called ferrite and is a body centered cubic (BCC) structure. The hardest phase is martensite, which is a body centered tetragonal (BCT) structure. Both of these phases are magnetic. When steel is heated above a critical temperature (about 1400F) it turns into a structure called austenite which is face centered cubic (FCC) structure and is nonmagnetic. The other two phases (pearlite and bainite) are ferrite plus a compound known as iron carbide (Fe3C). We will deal with ferrite, martensite and austenite.
In order to harden steel it must have a minimum of 0.25% carbon; less than that and it cannot form martensite.
Steps to Harden Steel
There are four steps to successfully harden steel:
1. Heat above the critical (phase change or transformation) temperature.
2. Hold at that temperature long enough for all of the material to form austenite.
3. Quench quickly enough to form martensite.
4. When the steel cools to about 250F – 300F reheat it to temper it.
Tempering relieves any internal stresses caused by untransformed martensite and while it reduces the maximum hardness a little it imparts toughness and eliminates brittleness and imparts some ductility into the material. The higher the tempering temperature the more hardness is reduced and the ductility increased so the desired hardness and ductility level must be based on the tempering temperature.
Steps to Anneal Steel
If it is desired to soften steel (to make it more ductile for forming operations or make it easier to machine) three steps are required:
1. Heat above the critical (phase change or transformation) temperature.
2. Hold at that temperature long enough for all of the material to form austenite.
3. Quench slowly enough to form ferrite.
It is standard practice to take steel that has not been annealed and soften it for machining, forming or welding by annealing it and then hardening it to reach the desired hardness and strength level.
Below is a diagram that shows what happens during the cooling of steel from the austenitic phase. The vertical axis shows temperature in Celsius, the horizontal axis is time (note that it is not linear but logarithmic). The green line is the transformation start temperature, the black line is the transformation end temperature. If the material cools quickly enough to miss the knee or nose of the transformation start temperature it will turn into martensite at about 220C (about 425F). If it cools slowly enough to pass through the transformation curve it will turn into one of the ferritic structures (bainite or pearlite). Plain carbon steel must cool in just a few seconds to form martensite as shown by the water or oil quench curve; letting it air cool will anneal the steel.
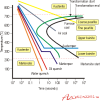
Alloy Steels
Just about any alloying element will push the nose or knee of the transformation curve to the right and allow the steel to be cooled slower and still reach maximum hardness. Plain carbon steel must be cooled so quickly that it is usually considered a water hardening steel, The need for rapid cooling limits the size or thickness of the steel; too thick and the inside cannot cool quick enough. It can also cause cracking. Moderately alloyed steel is often oil quenched which reduces the chance of cracking. Highly alloyed steels can often be air cooled and still harden fully. Conversely, plain carbon steel can be annealed just by air cooling it, whereas alloyed steels must be cooled far more slowly to anneal. Some air hardening steels must be cooled in the furnace by reducing the temperature of the oven slowly over an extended period, sometimes as long as 12 to 24 hours. (This explains the higher cost of air hardening tool steels; not only do the alloying element increase the cost, the time and energy costs drive up the price.)
Carbon steels can turn into austenite in just a few seconds. The more alloying elements there are in steel the longer it takes to turn into austenite. Remember that steel must turn completely into austenite so that it can turn completely into martensite
Handy tip: To make sure the steel has completely turned into austenite test it with a magnet – when the steel is no longer attracted to a magnet it is austenite.
Carbon and alloy steel numbering system
The AISI (American Iron and Steel Institute) and the SAE (Society of Automotive Engineers) use a four (or sometime five) digit numbering system to classify steels. The automotive industry is one of the largest consumers of steel, thus their input. The first two digits are the alloy type, the last two (or three) digits represent the carbon content in 0.1% Thus a plain carbon steel such as 1045 has a 10 to represent a plain carbon steel and the 45 represents 0.45% carbon. This is a hardenable steel because it has more than 0.25% carbon. A steel such as 1018 has too low a carbon content to harden. If you want to make it harder you must infuse carbon into the surface by case hardening it.
(Many early guns were made from low carbon steels and then wear parts such as the trigger and sear were case hardened. Case hardening is not very deep so too much metal removal can often cut through that layer and leave the resulting surfaces too soft for long use.)
Here is a chart of AISI/SAE steels grades:
Description | Designation | Composition |
Carbon Steel | 10XX | Plain carbon, Mn 1.00% max |
| 11XX | Resulfurized free machining |
| 12XX | Resulfurized/rephosphorized free machining |
| 15XX | Plain carbon, Mn 1.00 – 1.65% |
Manganese steels | 13XX | Mn 1.75% |
Nickel steels | 23XX | Ni 3.50% |
| 25XX | Ni 5.00% |
N9ckel Chromium steels | 31XX | Ni 1.25% Cr-.65% to 0.80% |
| 32XX | Ni 1.75% Cr 1.07% |
| 33XX | Ni 3.5% Cr 1.50 to 1.57% |
| 34XX | Ni 3.00% Cr 0.77% |
Molybdenum steels | 40XX | Mo 0.20% to 0.25% |
| 44XX | Mo 0.40% to 0.52% |
Chromium Molybdenum steels | 41XX | Cr 0.50% to 0.95% Mo 0.12% to 0.30% |
Nickel Chromium Molybdenum steels | 43XX | Ni 1.82% Cr 0.50% to 0.80% Mo 0.25% |
| 47XX | Ni 1.05% Cr 0.45% Mo 0.20% to 0.25% |
Nickel Molybdenum steels | 46XX | Ni 0.85% to 1.82% Mo 0.20% to 0.25% |
| 48XX | Ni 3.50% Mo 0.25% |
Chromium steels | 50XX | Cr 0.27% to 0.65% |
| 51XX | Cr 0.80% to 1.05% |
| 50XXX | Cr 0.50% C 1.00 minimum |
| 51XXX | Cr 1.02% C 1.00% minimum |
| 52XXX | Cr 1.45% C 1.00% minimum |
Chromium Vanadium steels | 61XX | Cr 0.60% to 0.95% V 0.10% to 0.15% |
Tungsten Chromium steels | 72XX | W 1.75% Cr 0/75% |
Nickel Chromium Molybdenum steels | 81XX | Ni 0.30% Cr 0.40% Mo 0.12% |
| 86XX | Ni 0.55% Cr 0.50% Mo 0.20% |
| 87XX | Ni 0.55% Cr 0.50% Mo 0.25% |
| 88XX | Ni 0.55% Cr 0.50% Mo 0.35% |
Silicon Manganese steels | 92XX | Si 1.40% to 2.00% Mn 0.65% to 0.85% Cr 0.65% |
Nickel Chromium Molybdenum steels | 93XX | Ni 3.25% Cr 1.20% Mo 0.12% |
| 94XX | Ni 0.45% Cr 0.40% Mo 0.12% |
| 97XX | Ni 0.55% Cr 0.20% Mo 0.20% |
| 98XX | Ni 1.00% Cr 0.80% Mo 0.25% |
Attachments
Last edited: