JonB
Halcyon member
Last week, I lucked into a big buy of 41 mag stuff.
All I wanted from this lot was the 500 pcs of brass and a RCBS seater die.
Well, besides the brass, there was a full set of RCBS dies with both carbide sizer and steel sizer. Also, there was several hundred 41 cal bullets, some jacketed, A good sized box of mixed Lyman GCs (45,41,357,22) about 1000 each, and this dang mold (Lyman 2 cav. 410610).
I shouldn't have even tried casting with it. I didn't really need it, I should have just sold it, because I did just get an awesome Arsenal 41 SWC mold.
Why is it, that a mold that I don't need just can't be left alone?
...especially a Lyman, I'm just not a big fan...but it did come with about 1k GC that should fit it.
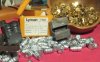
The first batch I cast, looked kinda ugly. The GCs fit snug, real snug, in fact some of the bullets were a no go. I assumed some of the ugliness was due to the remnants of spray-on mold release in the cavities, that I was unable to clean out.
So I decided to Lee-Ment the mold, of course, the fact the mold wasn't dropping the bullets without a swift whack, helped my decision.
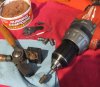
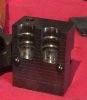
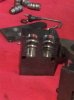
FYI, if you notice this block has more area that shines, this block was the sticky block.
...
Now for the reason I made this long post, and the lesson that I learned these last few days (five different casting sessions using three different alloys). How to cast a bullet so the GC shank is not over sized (with a mold that was cut right at the edge of being oversized).
I tried a few things:
An alloy with a lower percentage of antimony than my usual COWW.
Casting with a hot alloy, and then lowering the temp.
Then casting at a fast pace, then a slow pace, leaving the bullets in the cavities as long as possible, then dropping them right away.
I knew hotter was the way to go, then I though of slowing the stream (reducing head pressure)....aaaaaaand, that was the ticket!
But to get good fillout, I needed to run the mold hotter than I usually do and I jacked up the alloy temp to 730º, I've never run alloy that hot.
So, I slowed the stream of molten alloy from my Lee bottom pour furnace into the mold as much as possible, but still maintain a steady stream and not a dripping stream (having the 20 lb pot only filled half way, helped with this). The three frosty bullets on the Right were cast that way and the old lyman GCs I got with this purchase fit perfectly. That alloy was COWW. The edges are surely not sharp as the other three bullets, but the frosty ones are uniform.
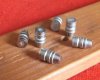
The three bullets on the left were from the first casting session with a range scrap alloy, temp set to 665º with a strong alloy stream into the mold, GCs were a no go with those three, as well as about half of the bullets from that batch. I would have measured the GC shanks, but they are tapered and I couldn't get reliable measurements.
Bullet diameter:
The interesting thing with this ...all the bullets that were cast after Lee-Menting, measured .413 whether I used the slow stream technique or not. I find it interesting that the slow stream technique reduced the size of the GC shank, but didn't reduce the band diameter, that I could measure, anyway?
All I wanted from this lot was the 500 pcs of brass and a RCBS seater die.
Well, besides the brass, there was a full set of RCBS dies with both carbide sizer and steel sizer. Also, there was several hundred 41 cal bullets, some jacketed, A good sized box of mixed Lyman GCs (45,41,357,22) about 1000 each, and this dang mold (Lyman 2 cav. 410610).
I shouldn't have even tried casting with it. I didn't really need it, I should have just sold it, because I did just get an awesome Arsenal 41 SWC mold.
Why is it, that a mold that I don't need just can't be left alone?
...especially a Lyman, I'm just not a big fan...but it did come with about 1k GC that should fit it.
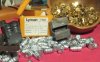
The first batch I cast, looked kinda ugly. The GCs fit snug, real snug, in fact some of the bullets were a no go. I assumed some of the ugliness was due to the remnants of spray-on mold release in the cavities, that I was unable to clean out.
So I decided to Lee-Ment the mold, of course, the fact the mold wasn't dropping the bullets without a swift whack, helped my decision.
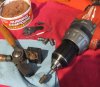
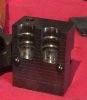
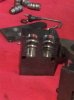
FYI, if you notice this block has more area that shines, this block was the sticky block.
...
Now for the reason I made this long post, and the lesson that I learned these last few days (five different casting sessions using three different alloys). How to cast a bullet so the GC shank is not over sized (with a mold that was cut right at the edge of being oversized).
I tried a few things:
An alloy with a lower percentage of antimony than my usual COWW.
Casting with a hot alloy, and then lowering the temp.
Then casting at a fast pace, then a slow pace, leaving the bullets in the cavities as long as possible, then dropping them right away.
I knew hotter was the way to go, then I though of slowing the stream (reducing head pressure)....aaaaaaand, that was the ticket!
But to get good fillout, I needed to run the mold hotter than I usually do and I jacked up the alloy temp to 730º, I've never run alloy that hot.
So, I slowed the stream of molten alloy from my Lee bottom pour furnace into the mold as much as possible, but still maintain a steady stream and not a dripping stream (having the 20 lb pot only filled half way, helped with this). The three frosty bullets on the Right were cast that way and the old lyman GCs I got with this purchase fit perfectly. That alloy was COWW. The edges are surely not sharp as the other three bullets, but the frosty ones are uniform.
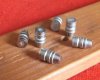
The three bullets on the left were from the first casting session with a range scrap alloy, temp set to 665º with a strong alloy stream into the mold, GCs were a no go with those three, as well as about half of the bullets from that batch. I would have measured the GC shanks, but they are tapered and I couldn't get reliable measurements.
Bullet diameter:
The interesting thing with this ...all the bullets that were cast after Lee-Menting, measured .413 whether I used the slow stream technique or not. I find it interesting that the slow stream technique reduced the size of the GC shank, but didn't reduce the band diameter, that I could measure, anyway?