KeithB
Resident Half Fast Machinist
As we prepare for our upcoming move one of the things I wanted to make was some anti-vibration mounts for our air compressors and rotophase unit. When I recently swapped out our old compressor for a new one I mounted it directly to the concrete floor. The old one had been mounted on 2" thick oak blocks, it helped quiet things down and it raised the drain valve underneath enough to make it easier to get to. The new one is a lot noisier.
I ordered a piece of 70 durometer Buna N rubber from Grainger. It was 1" thick, 4" wide, and 36" long. A thumb indent "test" gives me the feeling that it flexes about like a truck tire. (Maybe some of the mechanics here can tell me what hardness a truck tire measures.) It turned out there was no problem cutting it into blocks using a cutoff bandsaw and lots of soluble oil. The problem was trying to drill a 3/4" hole in the middle. Twist drills just tore things up, so after a little thought I bought a hole saw and tried it. Worked fine, except I had to take the drill off the arbor each time to remove the rubber plug inside. Took a couple holes to figure out exactly what to do. I took the twist drill out of the hole saw arbor, that left a solid plug, which I pushed out using an arbor press. I used air tool oil as a lubricant, it really helped push the plug out of the drill. Took a few minutes each time but the holes came out fairly clean.
I cut twelve pieces of 1/4" aluminum plate measuring 4" x 4" and eight pieces measuring 3" x 3". The larger pieces got a 3/4" hole drilled in the center, the smaller ones got a 1/2" hole. One side of the rubber sheet has an adhesive film covered by a tear-off strip of paper. I will put some double sided tape on the other side and stick an aluminum plate to each side to make a sandwich.
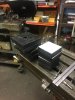
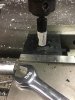
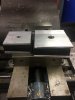
I ordered a piece of 70 durometer Buna N rubber from Grainger. It was 1" thick, 4" wide, and 36" long. A thumb indent "test" gives me the feeling that it flexes about like a truck tire. (Maybe some of the mechanics here can tell me what hardness a truck tire measures.) It turned out there was no problem cutting it into blocks using a cutoff bandsaw and lots of soluble oil. The problem was trying to drill a 3/4" hole in the middle. Twist drills just tore things up, so after a little thought I bought a hole saw and tried it. Worked fine, except I had to take the drill off the arbor each time to remove the rubber plug inside. Took a couple holes to figure out exactly what to do. I took the twist drill out of the hole saw arbor, that left a solid plug, which I pushed out using an arbor press. I used air tool oil as a lubricant, it really helped push the plug out of the drill. Took a few minutes each time but the holes came out fairly clean.
I cut twelve pieces of 1/4" aluminum plate measuring 4" x 4" and eight pieces measuring 3" x 3". The larger pieces got a 3/4" hole drilled in the center, the smaller ones got a 1/2" hole. One side of the rubber sheet has an adhesive film covered by a tear-off strip of paper. I will put some double sided tape on the other side and stick an aluminum plate to each side to make a sandwich.
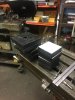
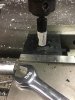
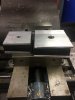