Dimner
Named Man
I need help with some advance math. I'm about 70% smurt enough to know that what I am looking for should be possible to calculate, but I have forgotten all of the 2 calc classes I took in college, and forgotten over half the trig from highschool.
What I'm looking for is the place along the nose of this bullet where the diameter is at 0.294. I don't own the bullet and this calculation will help me with my decision to purchase.
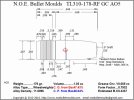
What I'm looking for is the place along the nose of this bullet where the diameter is at 0.294. I don't own the bullet and this calculation will help me with my decision to purchase.
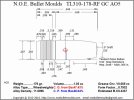