Ian
Notorious member
I wanted to experiment with hollow-point bullets in my .458 Socom AR-15 to see if I couldn't improve upon the subsonic lethal factor. Mastadons are out of season and pigs are in, so knock-down power is more important than raw penetration. Before spending a lot of money to have a good custom mould made and then hollow-pointed the Lee 500-grain RF two-cavity seemed a good place to start. Following what several others have reported I HP'd one cavity. First I did it with a 1/4" drill (and because I have a .250" chucking reamer) to match the original meplat. Tests showed the abruptly-round ogive wouldn't allow it to open up well, so I went to 5/16". Unfortunately no chucking reamer, so I drilled the hole and of course it's rough and oversized, but it works. Made the spud out of a brand new but too cheap to dare use bit that came "free" in a kit of some sort. Drill stop out of a Ryobi bit kit worked perfectly, as did a spare screw from a light fixture install kit.
Blue powder-coated bullet is a solid for comparison.
The insides and pin:
Couple of recovered test bullets fired at ~1000 fps. The wadcutter w/nose fragments was fired into a line of water jugs (hard clear plastic ones with screw on caps) and it went completely through six of them, completely exploding the first one and leaving the nose fragments inside and about the remains. The other jugs had neat holes poked through them and only #2 & #3 had their caps blown off. The slightly mushroomed bullet was fired through a tight roll of damp carpet (about 20 layers) and then into a row of the same water jugs, it went through four of them and popped out the side, found it on the ground about three feet away from where it exited. Not extremely scientific testing but what I had to work with on short notice.
Now I have a better idea of what will and won't work. The last iteration of this shortened the bullet enough that now the case shoulder gets dinged by the locking lugs of the barrel extension when chambering, so if I design a bullet for this it will be more of a WFN and have almost as long of a nose as the Lee solid. It's very interesting what very slight changes to bullet profile will do both to feeding and to point expansion, and I'm glad the price of tuition to that class was only $20 and a couple of afternoons tinkering with stuff I had laying around.
Blue powder-coated bullet is a solid for comparison.
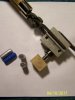
The insides and pin:
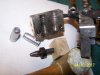
Couple of recovered test bullets fired at ~1000 fps. The wadcutter w/nose fragments was fired into a line of water jugs (hard clear plastic ones with screw on caps) and it went completely through six of them, completely exploding the first one and leaving the nose fragments inside and about the remains. The other jugs had neat holes poked through them and only #2 & #3 had their caps blown off. The slightly mushroomed bullet was fired through a tight roll of damp carpet (about 20 layers) and then into a row of the same water jugs, it went through four of them and popped out the side, found it on the ground about three feet away from where it exited. Not extremely scientific testing but what I had to work with on short notice.
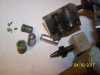
Now I have a better idea of what will and won't work. The last iteration of this shortened the bullet enough that now the case shoulder gets dinged by the locking lugs of the barrel extension when chambering, so if I design a bullet for this it will be more of a WFN and have almost as long of a nose as the Lee solid. It's very interesting what very slight changes to bullet profile will do both to feeding and to point expansion, and I'm glad the price of tuition to that class was only $20 and a couple of afternoons tinkering with stuff I had laying around.