KeithB
Resident Half Fast Machinist
I'm on a continuing quest to come up with the best way to cut threads quickly and accurately on a manual lathe. One way to do that is to use an expanding die head and the proper thread chasers. I'd bet that 99% of the threads I cut on a manual lathe are 5/8" diameter or smaller. Anything larger than that I can cut with a single point tool, so I determined that I needed a die head with that capacity. I found a used Rubometric (it's German) 9/16D die head on Ebay. I also found lots of used chasers on Ebay so I made sure when I bought an assortment that I got 1/2-20 and 3/8-24. Got a lot of other chasers also, but those two are the thread size on two products we make on the CNC lathe but could be made on a manual lathe.
The die head uses four chasers that can be changed out easily. In operation the die head is cocked, the rough/finish cut lever is flipped to the rough position and pushed on to the end of the rotating rod. The chasers cut and pull the die head forward. When the rear of the die head stops the front moves forward a short distance and then it automatically opens up. No need to stop or reverse the lathe spindle. Just push the die head back, recock it, flip the rough/finish cut lever to the finish position, and recut the thread to final size. The chasers cut the full profile including the top of the thread, so if the material is the proper size the thread crest is cut along with the flank and leaves no burr to be filed off. I threaded both ends of 32 3/8" rods (64 threads total) in about 2-1/2 hours. And I never even got out my thread file!
I needed a way to mount the die head to my lathe that would keep the head from rotating but allow it to move forward to a fixed repetitive location. The die head has a 5/8" straight shank. I made an adapter from a scrap piece of 4-1/4" aluminum round that would clamp on the OD of my tailstock quill. I also made a sliding sleeve that clamps onto the die head and that slides on a 5/8" rod that gets clamped into the tailstock adapter. Using this setup I can clamp my tailstock in place and control the length of threads. The die head moves forward until the slot in the sleeve hits a screw head in the shaft. The die head body stops moving forward and the die head front continues about 1/16" further before it trips and opens up.
The adapter to mount die head to tailstock quill.
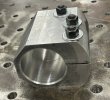
Rubometric die head
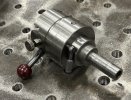
Die head showing slots for chasers
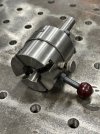
Die head mounted on lathe
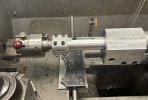
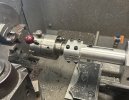
I'm really pleased with this tool, wish I'd bought one years ago!
The die head uses four chasers that can be changed out easily. In operation the die head is cocked, the rough/finish cut lever is flipped to the rough position and pushed on to the end of the rotating rod. The chasers cut and pull the die head forward. When the rear of the die head stops the front moves forward a short distance and then it automatically opens up. No need to stop or reverse the lathe spindle. Just push the die head back, recock it, flip the rough/finish cut lever to the finish position, and recut the thread to final size. The chasers cut the full profile including the top of the thread, so if the material is the proper size the thread crest is cut along with the flank and leaves no burr to be filed off. I threaded both ends of 32 3/8" rods (64 threads total) in about 2-1/2 hours. And I never even got out my thread file!
I needed a way to mount the die head to my lathe that would keep the head from rotating but allow it to move forward to a fixed repetitive location. The die head has a 5/8" straight shank. I made an adapter from a scrap piece of 4-1/4" aluminum round that would clamp on the OD of my tailstock quill. I also made a sliding sleeve that clamps onto the die head and that slides on a 5/8" rod that gets clamped into the tailstock adapter. Using this setup I can clamp my tailstock in place and control the length of threads. The die head moves forward until the slot in the sleeve hits a screw head in the shaft. The die head body stops moving forward and the die head front continues about 1/16" further before it trips and opens up.
The adapter to mount die head to tailstock quill.
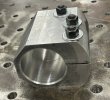
Rubometric die head
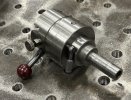
Die head showing slots for chasers
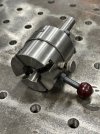
Die head mounted on lathe
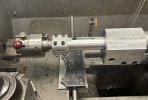
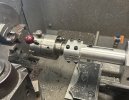
I'm really pleased with this tool, wish I'd bought one years ago!