Ian
Notorious member
I bought this unfinished kit from a member recently and finally got a chance tonight to inventory it and check it over. It's a very nice chunk of maple with strong curl from end to end and is shaped well for having come off of a duplicating machine. The 38" swamped Colrain barrel is fully and very nicely inlet and all filed out and the large Siler lock mostly inlet, it sits a little off the barrel flat because the flintcock is hitting wood that needs to be profiled off. The trigger guard, rammer thimble, and butt plate inlets are partially roughed out.
First thing to do is check barrel to lock alignment and then get the barrel tenons installed, inlet, drilled, and pinned. A check of the flash hole location brought me to the first problem: the barrel is too far forward for a flash hole liner. I assume the kit wasn't designed for one because one wasn't included, but I insist, so will have to set the barrel back about 3/16" to make it right. This poses two problems, first the kit barrel has a very chunky, flared tang not correct for the style it purports to be and moving it back induces gaps, and second, the barrel inlet will open up slightly in the back and bind in the front as the barrel is moved. Alao, Isaac Haines always fluted his tangs at the back, but that ship has sailed so we use what we got. I think I'll just live with the gap and square tang tail, mill 3/16" off of back of the tang, and inlet the barrel back the same amount. This will push the top of the tang proud of the stock but it needs to be thinned a bunch anyway. Fortunately no holes have been drilled in anything yet.
Here you can see the breech plug face location (forward edge of Sharpie line) and the FH location, the center of the FH and face of plug are 1/16" apart:
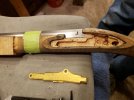
The vertical alignment of pan and barrel are perfect. It also appears that the front lock bolt will line up well with the web between the rammer hole and bottom of the barrel but I need to drill a small test hole in the bottom of the barrel channel to see how thick the web really is.
I had to laugh going through the parts when I discovered that Track's order picker put a right-hand side plate in this kit even though the paperwork clearly shows a LH one, so I'll be making a new one of out of cartridge brass bar. The nose cap and trigger/ bottom plate assembly are hopeless, so I will make a proper nose cap from sheet brass and am very seriously considering installing a double-set trigger assembly for it even though not correct for the build. At the least I will make a single trigger and pin it high in the stock with a new plate. Still mulling it over as a Siler lock with proper single-trigger geometry can result in a very nice trigger pull.
Once I get the barrel in, tang bolt drilled, lock fully situated, and both the lock bolts drilled I will move onto filing the buttplate and fitting it to the stock, then making a toe plate and fitting that, trigger guard, side plate, rammer thimbles, and finally the nose cap. After that I'll finish shaping the stock, install a four-piece patch box, shape the forearm and toe mouldings, and start the relief carving. This is going to be fun!
First thing to do is check barrel to lock alignment and then get the barrel tenons installed, inlet, drilled, and pinned. A check of the flash hole location brought me to the first problem: the barrel is too far forward for a flash hole liner. I assume the kit wasn't designed for one because one wasn't included, but I insist, so will have to set the barrel back about 3/16" to make it right. This poses two problems, first the kit barrel has a very chunky, flared tang not correct for the style it purports to be and moving it back induces gaps, and second, the barrel inlet will open up slightly in the back and bind in the front as the barrel is moved. Alao, Isaac Haines always fluted his tangs at the back, but that ship has sailed so we use what we got. I think I'll just live with the gap and square tang tail, mill 3/16" off of back of the tang, and inlet the barrel back the same amount. This will push the top of the tang proud of the stock but it needs to be thinned a bunch anyway. Fortunately no holes have been drilled in anything yet.
Here you can see the breech plug face location (forward edge of Sharpie line) and the FH location, the center of the FH and face of plug are 1/16" apart:
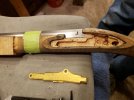
The vertical alignment of pan and barrel are perfect. It also appears that the front lock bolt will line up well with the web between the rammer hole and bottom of the barrel but I need to drill a small test hole in the bottom of the barrel channel to see how thick the web really is.
I had to laugh going through the parts when I discovered that Track's order picker put a right-hand side plate in this kit even though the paperwork clearly shows a LH one, so I'll be making a new one of out of cartridge brass bar. The nose cap and trigger/ bottom plate assembly are hopeless, so I will make a proper nose cap from sheet brass and am very seriously considering installing a double-set trigger assembly for it even though not correct for the build. At the least I will make a single trigger and pin it high in the stock with a new plate. Still mulling it over as a Siler lock with proper single-trigger geometry can result in a very nice trigger pull.
Once I get the barrel in, tang bolt drilled, lock fully situated, and both the lock bolts drilled I will move onto filing the buttplate and fitting it to the stock, then making a toe plate and fitting that, trigger guard, side plate, rammer thimbles, and finally the nose cap. After that I'll finish shaping the stock, install a four-piece patch box, shape the forearm and toe mouldings, and start the relief carving. This is going to be fun!