Ian
Notorious member
CoG thing is the same regardless of alloy. Miller changes a little because of density/length but it's in stability's favor.
The whole problem with Bismuth alloy is Bi is incredibly crystalline and brittle. The shear planes are the size of coins. Everything we add tends to refine it some, but the relative scale is still working against us. Lead is mush and we have to add stuff to reinforce it and then add other stuff to make the reinforcement mesh finer and tougher and other stuff still to make it cure better, but with Bi we only have slightly less tough stuff to add to it to refine and soften it and really it all becomes a game of controlled fracture.
I edited a little better photo here of the 88/12/.75 alloy's broken surface compared to 73/27/.56 after adding tin. This lowered the melt point about 100 degrees which makes it unsutable for shooting, and it was still brittle, so grain refinement isn't the whole key here to making Bismuth ductile. I really think dhat for practical purposes the 88/12 with a dash of Sb is as good as we're going to get, or at least as much effort as I'm willing to put into alloying at this point. What we have here is easily cast, sized, shoots well, and is ductile enough. The rest we can work around with bullet design.
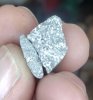
The whole problem with Bismuth alloy is Bi is incredibly crystalline and brittle. The shear planes are the size of coins. Everything we add tends to refine it some, but the relative scale is still working against us. Lead is mush and we have to add stuff to reinforce it and then add other stuff to make the reinforcement mesh finer and tougher and other stuff still to make it cure better, but with Bi we only have slightly less tough stuff to add to it to refine and soften it and really it all becomes a game of controlled fracture.
I edited a little better photo here of the 88/12/.75 alloy's broken surface compared to 73/27/.56 after adding tin. This lowered the melt point about 100 degrees which makes it unsutable for shooting, and it was still brittle, so grain refinement isn't the whole key here to making Bismuth ductile. I really think dhat for practical purposes the 88/12 with a dash of Sb is as good as we're going to get, or at least as much effort as I'm willing to put into alloying at this point. What we have here is easily cast, sized, shoots well, and is ductile enough. The rest we can work around with bullet design.
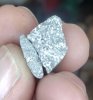