Ian
Notorious member
Well, one of many reasons: It gets the junk out and leaves the good stuff in the casting pot.
Ever since reading Glen's article "The 'Simple' act of Fluxing" years ago and subsequently experimenting a great deal with various sorts of sawdust, shavings, pine resin, coffee grounds, wheat bran, stale breakfast cereal, sugar, and other things from the shop and pantry, my success rate using dirty, contaminated lead scrap for bullet casting has improved drastically.
Here are a couple of photos of what yellow pine debitage from underneath the router table can do to a pie plate full of skimmings saved up from multiple casting sessions with a batch of very ornery clip-on wheel weight alloy. I didn't flux at all during all that casting, just stirred vigorously to make a vortex and spooned-off the big mats of dross that accumulated and saved them. The alloy didn't flow well and cast small, so anything that floated I wanted OUT and not fluxed back in. All of those sessions were run by dumping sprues back in the pot as I went, so oxide accumulation was heavy. I took the 1/3-full pie plate of accumulated dross and dumped it all into 1/3 pot of same alloy, added a full cup of shavings, let it heat up until the shavings were smoking, then lit the fumes and let it burn while "turning" the mushy mat of goop over and over through the burning wood with a spoon. Just about the time the flames burned out I squeezed out most of the good alloy and skimmed the dirt, bigger bits of charcoal, and ash. I was amazed at how much "heavy dirt" came out; stuff that didn't reduce. All the clean lead alloy went back into solution except for the few little nuggets that got trapped with the spoon when skimming the ashes. You can see the little nuggets retrieved from the mess after it cooled, and the "dirt", and the charcoal. I don't know what's in that dirt stuff but it made it through one remelt/cleaning/ingotizing and a casting session before being reduced to metal again and the alloy resulting from reducing all that dross casts MUCH better now.
Can your beeswax do this?
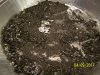
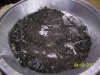
Ever since reading Glen's article "The 'Simple' act of Fluxing" years ago and subsequently experimenting a great deal with various sorts of sawdust, shavings, pine resin, coffee grounds, wheat bran, stale breakfast cereal, sugar, and other things from the shop and pantry, my success rate using dirty, contaminated lead scrap for bullet casting has improved drastically.
Here are a couple of photos of what yellow pine debitage from underneath the router table can do to a pie plate full of skimmings saved up from multiple casting sessions with a batch of very ornery clip-on wheel weight alloy. I didn't flux at all during all that casting, just stirred vigorously to make a vortex and spooned-off the big mats of dross that accumulated and saved them. The alloy didn't flow well and cast small, so anything that floated I wanted OUT and not fluxed back in. All of those sessions were run by dumping sprues back in the pot as I went, so oxide accumulation was heavy. I took the 1/3-full pie plate of accumulated dross and dumped it all into 1/3 pot of same alloy, added a full cup of shavings, let it heat up until the shavings were smoking, then lit the fumes and let it burn while "turning" the mushy mat of goop over and over through the burning wood with a spoon. Just about the time the flames burned out I squeezed out most of the good alloy and skimmed the dirt, bigger bits of charcoal, and ash. I was amazed at how much "heavy dirt" came out; stuff that didn't reduce. All the clean lead alloy went back into solution except for the few little nuggets that got trapped with the spoon when skimming the ashes. You can see the little nuggets retrieved from the mess after it cooled, and the "dirt", and the charcoal. I don't know what's in that dirt stuff but it made it through one remelt/cleaning/ingotizing and a casting session before being reduced to metal again and the alloy resulting from reducing all that dross casts MUCH better now.
Can your beeswax do this?
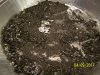
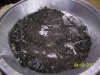